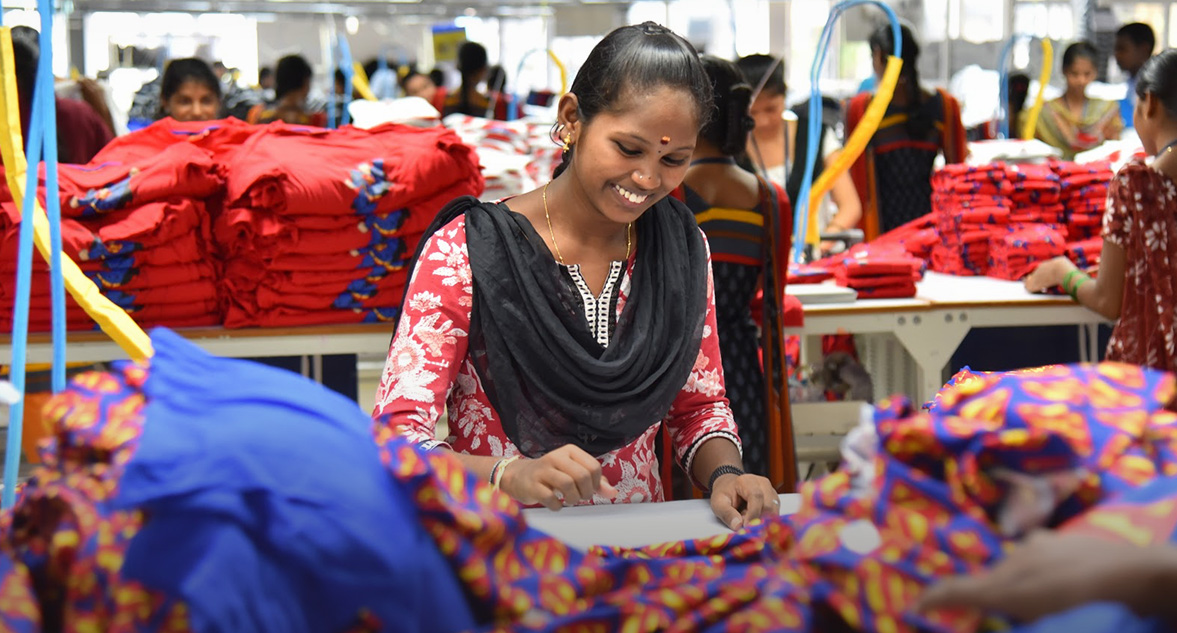
Responsible Manufacturing
Thousands of people are involved in producing our garments - around 170 millions of products were produced in 2022 -, a job that offers stable employment opportunities in countries where the textile industry is the biggest driving force for development. We guarantee the very best standards on human rights and working conditions and collaborate with our suppliers to continuously improve their practices and technology, so that we can help produce a positive impact in the countries where we operate.
Our supply chain spans 16 countries and more than 600 suppliers, with whom we are in constant contact through our sourcing offices.
The average time we have been working with our suppliers is not less than 9 years.
More than 90,000 workers are employed to produce our garments, and more than half of them are women. That being said, there is still a large gender gap in terms of supervisory and managerial roles, which are predominantly occupied by men.
You can see where our suppliers are located on the interactive Open Supply Hub platform.
Males | Females | |
---|---|---|
Workers | 31% | 69% |
Assistants | 68% | 32% |
Supervisors | 82% | 18% |
Line Chiefs | 82% | 18% |
Support personnel | 81% | 19% |
Cleaning | 54% | 46% |
Administration & Management | 73% | 27% |
From a social perspective, OVS' Supply chain (represented in the table above) shows more than half of the workers in the textile industry are women, but this majority is unbalanced in favor of high male percentages in supervisory and managerial roles.
Such a complex ecosystem requires high standards, measurement procedures, and control systems.
CODE OF CONDUCT
We only work with companies that share and abide by our values, with the hope that our guidelines are used as a tool for continuous improvement rather than a mere list of directives.
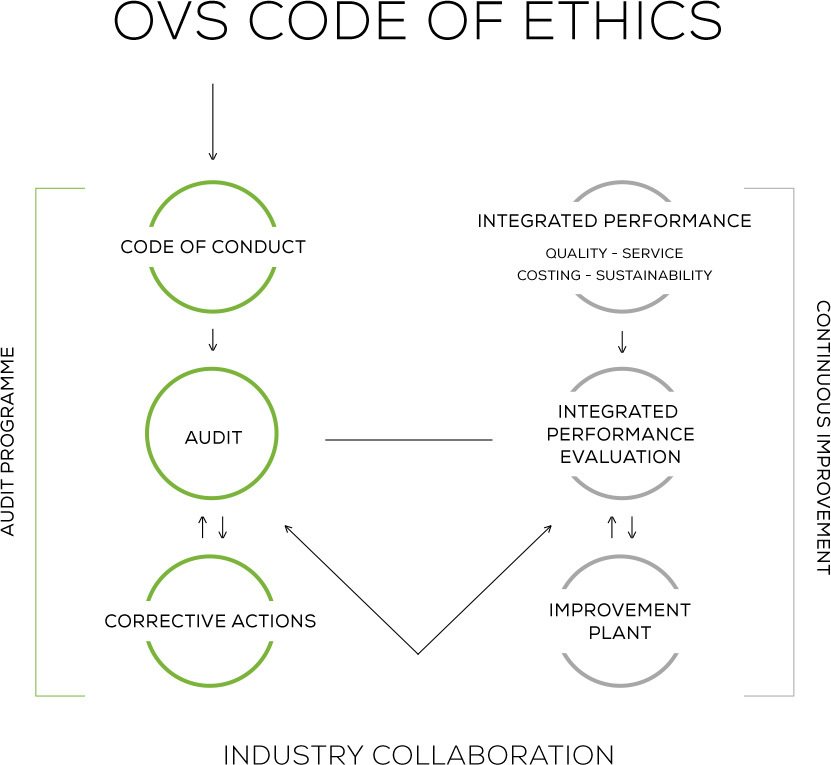
Our Code of Conduct lists the values that inspire all of our actions, as well as a set of operational guidelines on social, environmental and transparency issues.
OUR CODE OF CONDUCT IS A SET OF BINDING GUIDELINES REGARDING THE ENVIRONMENT, COMMUNITY AND PERFORMANCE IN ORDER TO IMPROVE SUPPLIER TRANSPARENCY AND SUSTAINABILITY LEVELS OVER TIME.
Our Code of Conduct ensures that everyone takes responsibility in the creation of an ethical circle at an economic, environmental and social level, contributing to improving working conditions with positive effects on local communities.
All suppliers who work with OVS are required to sign the Code of Conduct.
Each supplier is sent a graphic document to hang on their company’s premises, translated into the local language, that summarizes the main point of the code of conduct to be followed so all workers are aware of their rights. (Link at bottom of page for download).
The actual placement of the document is verified by our staff during visits to the factory. The local language document sets forth the email address for workers to make reports. During 2020, one report was received from a generic email address and lacking minimal information content for which additional information was requested. However, the reporter did not provide any further feedback. We received no reports in 2021 and 2022.
SUPPLIERS EVALUATION
When evaluating our suppliers, we give as much importance to sustainability as we do to our primary assessment criteria (Quality, Service and Cost). With a view to transparency and collaboration, we openly share the results of our assessments with factories, in order to identify areas for mutual improvement. We pair our Vendor Rating system with an audit initiative, which is carried out in several different areas in order to verify effective compliance with our Code of Conduct and to measure our suppliers’ environmental and social performance.
In general OVS does not allow the use of sub-contracting except in cases where this is expressly authorized. In order to maintain control of this constraint, OVS each season collects from each supplier a map of the production sources used both for the packaging processes and for the main production phases and the most important raw materials. After that, OVS sends inspectors to check the quality and progress of production.
Since 2020, each new supplier is confirmed only if they share their data on the online HIGG Index.
AUDIT
Before starting the supply and then every 12/18 months (unless a higher frequency is required), every factory is evaluated with respect to its compliance with the code of conduct and its environmental / social performance. All of our audits (561 in 2021 and 410 in 2022 - that covered 90% of production volume) are semi-announced, agreeing on a time window for audit activity but not specifying a visit date. When necessary, we also perform unannounced audits (3 in 2021) to investigate situations more thoroughly.
In addition Higg checks were made in one unannounced case 32 semi-announced and the rest announced.
The integrated supplier assessment is carried out using all available information gathered through certificates issued by independent third parties, analysing the performance data on HIGG and considering any reports received from trade unions or other associations.
This information is supplemented by direct checks by our staff and / or external auditors. If critical issues are identified, an action plan is agreed upon with the factory managers to fix them.
In any case, any critical issues identified are shared with workers' representatives to keep them informed of developments and to receive any feedback.
In order to have a better representation of the factories, in 2022 we decided to systematize the involvement of workers representatives, both as the integral part of the interviews conducted in the factories and in the review of the evidence of the audit results.
Following the priority by the production volume of the countries, we are systematizing the data collection starting from Bangladesh where today the workers’ representative has been involved in 22% of our audits.
Moreover, with the same purpose we have chosen to interview some workers outside the factories, integrating the interviews that were conducted inside. We prioritize Myanmar where we found that 100% of the interviews were conducted outside the factory, covering approximately 1% of the total workforce of all our suppliers.
In 2023, more data will also be available relating to other production areas.
FEM AND FSLM HIGG MODULES
The average aggregated audit score on the Higg Facility Environmental Module (FEM) in 2021 was 50% and in 2022 42%, while for the Higg Facility Social and Labor Module (FSLM) was 73% and in 2022 is 60%.
The average aggregate score achieved by Tier 2 suppliers on the FEM in 2021 is 60%, in 2022 is 60.8% for the FEM and 42% for the FSLM.
Suppliers' commitment in monitoring social and environmental performance is a significant contribution to improve OVS's transparency and helping to achieve the sustainability objectives set out in the annual plan. In order to recognise the path taken and provide an incentive for continuous improvement, in 2021 we awarded the best performing suppliers with the "Best suppliers 2021" plaque. For 2021, Tier 1 suppliers chosen were: Montex Fabrics Limited in Bangladesh, Zhejiang Yige in China, Master Textile Mills Limited in Pakistan and KPR Mill Limited in India.
The analysis of the FSLM module on Higg allowed us to identify some specific risks, in particular those concerning gender-related violations of workers' rights. Using this performance assessment tool, by analyzing some indicators, we identified that 3% of production sources reported cases of gender-related violations, in particular cases of physical abuse and failure to protect labor rights of female workers during maternity leave.
PURCHASING PRACTICES
OVS adopts responsible purchasing practices throughout its supply chain to reduce any negative social or economic impact on the industry workers, always paying attention to agree conditions with the supplier so that they operate safely and consistently with the various compliance requirements (for example: avoiding changes of orders when in production, paying the amount due with the agreed terms, etc.).
Due to Covid-19, we changed the payment terms for 16% of orders that had already been sent to suppliers in 2021.
The 67.7% of the volume purchased is paid through Letter of Credit, opened at the same time as the order is issued and therefore in advance of production activities, which allows the supplier to finance itself at banking institutions to cover the cost of purchasing materials. On average, the number of days in which the payment is completed was 116 days in 2020.
On a seasonal basis, we analyze the main cost trends related to raw materials, transport, duties, etc. in order to take them into account when defining the target costs, so that we can always ensure proper negotiation. Over the last twelve months, to take into account these changes in purchasing conditions, the average percentage increase of FOB prices was 7.5%.
OVS has defined its own Responsible Purchasing Policy, which serves as a guide in procurement activities. (See annex)
During the last survey on the level of satisfaction in the commercial relationship with OVS (considering payments, timely payments, ease of communication and proper production planning) 93% of suppliers declared themselves Satisfied or More than satisfied.
58% of orders are placed with suppliers, whose salary situation is known by us, thus managing to isolate the cost of labor which depends on several factors (type of products, the process performed, the efficiency rate and the technological innovation levels of the plants).
We chose to analyze the levels for each factory payroll and use these data during open-cost negotiations with suppliers. This allows us to identify possible discrepancies between the declared level cost and wage level conditions of the workers. During the periodic audit activity these salary data are subject to review by our auditors
SALARY CONDITIONS
At OVS, we know that we have a duty to act responsibly during the product purchasing phase, even though we don’t pay our suppliers directly. That’s why we regularly analyse wage conditions along our supply chain.
At present, from our analyses, that cover 67% of production volume it results that:
- 79% of workers are paid by bank transfer,
- no worker is paid below the legal minimum wage
- 70% of workers are paid an average of 33% more than the minimum guaranteed by law.
However, in some countries there is still a gap between the living wage and the legal minimum wage.
The living wage guarantees employees and their families a decent standard of living and is a human right recognised by the United Nations. The living wage is earned in a standard 48-hour working week and covers necessary expenses such as food, accommodation, education, health care, transport, and small savings for unforeseen events.
OVS is working to improve the quality of available data in order to allow for a more accurate analysis of wage conditions in its supply chain.
We are aware that in some situations this salary threshold may be lower than the Living Wage benchmark, and for this reason we have taken specific steps to analyze the data more effectively, integrating into our supplier assessment program an analysis dedicated to the salaries actually paid to workers and comparing them to the Global Living Wage Coalition benchmark. In addition, when negotiating with new suppliers, OVS analyses the impact of labour costs on the overall product cost to make sure there are no critical wage issues.
In 2021, we conducted wage analysis on more than 430 factories employing a total workforce of 415,000 people. We assessed average wages by job category compared with the Global Living Wage Coalition's Living Wage benchmark.
We found that the wages of 40% of workers involved in the supply chain were below the living wage threshold, despite widespread compliance with national minimum wage requirements.
Approximately 98% of workers in China, 99% in Pakistan, and 65% in India receive the living wage, as a minimum.
The most significant difference, however, occurs in Bangladesh where only 13% of workers receive a living wage. The remaining 87% receive a wage, which, although higher than the minimum wage, is still lower than the living wage by about 40% on average.
Furthermore, we have partially estimated in our supply chain the number of workers paid for piece-rate, we report the data in percentage:
- North India: 6% of workers
- South India: 12% of workers
- Bangladesh: 1.7% of workers
From our analyses, we have no evidence that these categories of workers are paid below the minimum wage.
Although there is still a long way to go, we have been witnessing a steady increase in wages for some time now, as well as a rapid improvement in working conditions in our manufacturing countries. This is a consequence of the textile industry maturing to become increasingly responsible and capable of involving its suppliers in development schemes.
The annual increase in average wages since 2019 has been 13% in Bangladesh, 34% in India and 31% in Pakistan.
The figures above represent a challenge that OVS is ready to take on, fully aware that our responsible business approach has had an important positive impact on the geographical region and its social fabric, also thanks to the consolidation of commercial relations with the most socially aware suppliers.
Unfortunately, buyers can only indirectly affect wages, as they tend to depend on local government choices, manual labour productivity, and labour market dynamics.
Although this is partly the result of economic policy, one of the main reasons for below-minimum wages is the lack of trade union agreements due to poor worker representation in wage bargaining. As such, we believe that these mechanisms can help progressively raise wages to the living wage.
TRADE UNION, WPC AND COLLECTIVE BARGAINING
Based on the data we have analyzed, we estimate that 18,5% of our suppliers - corresponding to 20% of production volume - have at least one form of workers representation, democratically elected, 5% of which are trade unions.
Moreover, we estimate that 7% of the workers are covered by collective bargaining. In some cases - 9 in India, 10 in China and 1 in Bangladesh - there are collective bargainings that negotiate higher wages than the legal minimum wage.
We have found violations of the freedom of association of workers, excluding China, in 1.6% of our suppliers - which represents 4% of the production volume - mainly related to the functioning of the workers' bipartite committees.
Although workers in China had the right to form or join a trade union, that right was limited because all unions, as per the Trade Union law of China, must be affiliated with the All-China Federation of Trade Unions (ACFTU).
The updated list of trade unions present in some factories up to 2022 is integrated in the Tier 1 list (see TIER 1 SUPPLIER LIST you can download at the bottom of the page).
Considering the above, we have set the following medium-long term objectives:
- by 2025, 50% of the production volume covered by suppliers who have democratically elected workers' representative bodies, thus giving workers the opportunity to align their remuneration with a wage level consistent with the actual cost of living;
- by 2030, 100% of the production volume will be covered by suppliers who have some form of workers’ representation.
Up today, 39% of the suppliers we work with have an operating grievance mechanism system and for this reason we aim to encourage its extension up to 50% of suppliers by 2025, to reach 100% in 2030.
Thanks to these actions, workers' pay conditions will gradually improve over time and we aim for all workers in our supply chain to receive a living wage by 2040.
To achieve these objectives, we have identified the main levers that can be exploited by OVS and its suppliers.
OVS's influence on suppliers | OVS’s areas of intervention |
---|---|
|
|
ADDRESSING HUMAN RIGHTS IN KEY AREAS OF SUPPLY CHAIN
Towards a living wage in Bangladesh
OVS manufactures millions of products through its global supply chain, providing thousands of people with jobs that offer stable employment in countries where the textile industry is a significant driver of development. We are committed to upholding the highest standards in human rights and working conditions. We collaborate with our suppliers to continually enhance their practices and technology, thus contributing to a positive impact in the countries where we operate.
Our suppliers in Bangladesh are valuable partners, sharing a strong and enduring relationship with us for more than twenty years, and they align with our commitment by signing our Code of Conduct.
OVS has contributed to several initiatives with an important impact on workers rights. From the beginning OVS was a signatory to Accord on Fire and Building safety and recently joined the EIS Pilot program run by ILO to establish an injury insurance system. Finally, together with the Circular Fashion Partnership, OVS is also contributing to the development of a circular economy system.
We understand that a living wage is not regulated in many countries, and national minimum wages in Bangladesh need to be improved in order to align to a recognized living wage benchmark.
The right to a decent salary is a fundamental right for workers. We are not entitled to define the level for a living wage, but we are committed to supporting any initiatives aimed at progressively granting this right to all workers, established through a negotiation process with all stakeholders involved.
Our business relationships in Bangladesh have been successful over the years and throughout a continuous social and economic evolution. Our purchasing practices and contractual documentation requires all prices to be comprehensive of all the costs necessary to maintain a responsible business conduct. We do not see any reasons to alter our production allocation unless unforeseen disruptions arise that hinder us from maintaining this approach.
Enabling effective freedom of association and collective bargaining is crucial in achieving a salary that progressively aligns with the living cost.
Therefore, we strongly condemn any potential repression or harassment of union representatives, as they play a vital role in pursuing the aforementioned goal of ensuring a living wage for all workers.
Forced labour in Xinjiang
OVS has joined the call to action launched by the Clean Clothes Campaign to End Uyghur Forced Labour and other forms of abuse against Uyghur people in the Xinjiang region of China.
The program provides for the suspension of all activities in the region of Xinjiang with the aim of raising awareness and requesting the Chinese government and Chinese companies concerned, the implementation of significant changes regarding the protection of Human Rights and the permanent cessation of forced labor.
OVS has identified four potential situations that could cause the company to trigger exit procedures and terminate its supply contracts:
- the supplier is located in the Xinjiang region;
- the supplier has branches in the Xinjiang region;
- the supplier is located outside the Xinjiang region but employs Uyghur workers under labour 'export' programmes. In this case, contracts will be terminated following due diligence;
- the supplier is located outside the Xinjiang region but uses materials from the Xinjiang region for production.
Political crisis in Myanmar
Following the coup d'état in Myanmar in early 2021, OVS decided not to stop operations in the country because withdrawing production would have caused a further negative impact on workers.
The political crisis situation negatively impacted on the effectiveness of the due diligence process, so we decided to continue operations only with production sites that would ensure full visibility of procedures through multi-stakeholder initiatives (e.g. HIGG) and third-party audits.
In relation to the production of the Fall-Winter 2023 collection, OVS has decided to keep production running in Myanmar. This position will be reviewed before starting Spring-Summer 2024 production if there is evidence of unbearable violations that cannot be remedied due to a deteriorated local context. In that case, OVS will immediately implement a responsible exit plan.
In order to properly adapt the due diligence process to the country context, OVS is committed to working with its long-term manufacturing partners to:
- facilitate a direct and smooth dialogue between employers and workers;
- increase the frequency of the assessment with a third party audit every six months;
- establish randomly selected workers’ interviews on-site and off-site;
- collaborate with factories management to deploy a grievance mechanism through a mobile app to be installed on workers' smartphones to enable a direct and anonymous conversation with factories’ management;
- monitor real-time data about possible social risks, through the mobile platform.
Thanks to the approach adopted, we have recorded signs of improvement. One above all is the case of a supplier for which we supported the audit activity, despite having interrupted the orders. The remedy plan has led to several results, confirmed by some civil society organizations, including:
- integration of anti-discrimination and anti-violence policies with related training plans for managers and employees;
- integration of an anonymous system for reporting violations;
- reorganization of the team to better distribute workloads.
The case of a supplier in Bangladesh - Personnel and payroll management
Following a verification process, we identified one of our suppliers in Bangladesh as having a serious problem in the management of incorrectly tracked salary payments, because the structure lacked a payroll management system and trained personnel dedicated to this activity.
We therefore activated a consultant for a more detailed analysis and agreed with the factory owner on the implementation of a personnel management system.
The intervention was structured as follows:
Verification result:
- there is no control and verification system for salary payments.
Cause:
- there is a lack of a team responsible for managing personnel and payroll.
Remedial actions:
- hire a competent person dedicated to the factory to deal with compliance;
- organize a top management awareness session on workers' fundamental rights and benefits.
Results:
- the factory now has a competent person in charge of people management system;
- the level of awareness on fundamental rights and benefits for workers has increased;
- all workers receive their salaries through traceable payment systems.
ADDRESSING ENVIRONMENTAL RISKS IN KEY AREAS OF SUPPLY CHAIN
The case of a supplier in Bangladesh - Wastewater monitoring
During our regular supplier compliance audits, we found the absence of a wastewater monitoring system.
The intervention was structured as follows:
Outcomes of the evaluation:
- the facility does not have a wastewater monitoring system working properly.
Cause:
- the structure does not have a person dedicated to monitoring activities and does not organize training for staff.
Remedial actions:
- the facility shall conduct an assessment and organize the required training of responsible personnel based on the identified deficiencies;
- the factory must implement the wastewater monitoring system.
Results:
- implementation of the now properly functioning wastewater monitoring system controlled by a suitably trained person.
INDUSTRY COLLABORATION
Contributing to profound change in the sector means embracing a team logic that involves all market players, promoting development projects that affect the entire fashion industry.
With this in mind, we were the first Italian company to join the Sustainable Apparel Coalition.
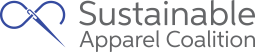
Discover more
The Sustainable Apparel Coalition is a progressive clothing, footwear and home-furnishing alliance, founded with the aim of promoting sustainable production.
We work with the Sustainable Apparel Coalition to create tools that measure environmental and social performance in the supply chain and raise transparency standards for the benefit of all stakeholders.
Since 2017, OVS has adopted HIGG Facility Tools, the digital platform of assessment tools in the clothing and footwear industry, developed by SAC to encourage the sharing of information with other companies in the supply chain.
Through the HiGG Facility Tools FEM (Facility Environmental Module) and FSLM (Facility Social Labour Module) online questionnaires, we measure the social and environmental performance of our suppliers’ facilities in order to improve the impact generated during production.
In line with our own principles, the Group's Code of Ethics and a range of global sustainable development goals, we’re attempting to build a reliable supply chain that respects the basic principles of dignity, health and safety of workers in countries where we operate, but primarily in Bangladesh, where OVS's main production site is located.
In addition to our standard supplier practices, we have participated in drafting an agreement (Accord) on fire and building safety in Bangladesh in order to ensure the necessary safety conditions for our workers.
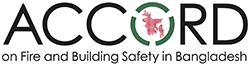
Discover more
Accord is a legally binding agreement between brands, manufacturing companies and local trade unions in order to promote greater health and safety in Bangladesh’s clothing industry, helping to create a safer working environment and prevent risks.
https://bangladeshaccord.org/During 2021, we launched new traceability systems along our supply chain, which allow us to analyse our suppliers in more detail.
The process of migrating to our new platform is still ongoing and our data are being updated as we speak. Missing information will be included in monthly updates based on the information we collect and cross-reference.
In addition, we are seeing some discrepancies emerge compared to data we had previously published. This is due to our improved classification system for production sources and different supply levels.
The lists of suppliers available here refer to those who worked for the autumn-winter 2022 and spring-summer 2023 collections.